O que é PCB de Cerâmica?
O que é PCB de Cerâmica?
A placa de circuito impresso de cerâmica também é chamada de substrato de cerâmica, placa de circuito de cerâmica, placa revestida de cobre de cerâmica, substrato de cerâmica refere-se à folha de cobre diretamente ligada ao substrato de cerâmica de alumina (Al2O3) ou nitreto de alumínio (AlN) ou a outra superfície de substrato de cerâmica (simples ou dupla) na placa de processo especial.
A PCB de cerâmica pode ser descrita como um aglutinante orgânico e um pó de cerâmica que conduz o calor. A condutividade térmica na qual essa PCB é preparada está entre 9 e 20W/m.
Para explicar melhor, as PCBs de cerâmica são placas de circuito impresso que têm a cerâmica como material de base. Esse material de base é altamente condutor de calor, como nitreto de alumínio, alumina e óxido de berílio. Esses materiais são muito eficazes na transferência de calor de pontos quentes e, em seguida, na dissipação desse calor por toda a superfície.
Além disso, a fabricação de PCBs de cerâmica é feita com a tecnologia LAM. Essa tecnologia é um tipo de metalização de ativação rápida a laser. Portanto, as PCBs de cerâmica são altamente versáteis e podem substituir facilmente todas as PCBs tradicionais. Essa placa de circuito impresso conseguirá isso com um desempenho ainda mais aprimorado e envolvendo uma construção menos complicada.
1. A diferença entre o substrato de cerâmica e PCB normal
Substrato cerâmico é o mesmo que placa de circuito cerâmico, placa de circuito impresso e placa de circuito impresso de cerâmica têm a mesma interconexão de circuito, através de características de condução de orifício. Então, quais são as diferenças entre o substrato de cerâmica e a placa de circuito impresso?
(1) A condutividade térmica da placa de circuito impresso e do substrato de cerâmica é diferente
O substrato de cerâmica é feito de substrato de cerâmica, ou seja, o meio é um material cerâmico, incluindo base de cerâmica de alumina, base de cerâmica de nitreto de alumínio, base de cerâmica de nitreto de silício, o desempenho de dissipação de calor da cerâmica é muito bom, a condutividade térmica do substrato de cerâmica é de 25w a 230w, a condutividade térmica do meio cerâmico é diferente. A condutividade térmica do substrato de cerâmica de alumina é de 25 a 30 watts, a condutividade térmica do substrato de cerâmica de nitreto de alumínio é superior a 170 watts e a condutividade térmica do substrato de cerâmica de nitreto de silício é de 80 a 90 watts. Em seguida, a placa de circuito impresso geralmente usa o meio fr4 ou substrato de metal, a condutividade térmica é inferior a 3w e a lacuna é muito grande em comparação com o substrato de cerâmica, especialmente a necessidade de alto desempenho de dissipação de calor do campo do produto, o substrato de cerâmica se tornou um material médio muito popular.
(2) O substrato de cerâmica e o isolamento da placa de circuito impresso são diferentes
O substrato cerâmico é geralmente uma estrutura de camada de linha - base de cerâmica - camada de linha, o isolamento do substrato cerâmico é muito bom, também é determinado pelo próprio material cerâmico, não há necessidade de adicionar camada de isolamento. A placa de circuito impresso precisa adicionar uma camada isolante para desempenhar um papel de isolamento móvel, mas o efeito de isolamento é muito menor do que o do substrato cerâmico.
(3) A estrutura de dissipação de calor do substrato de cerâmica é diferente da estrutura da placa de circuito impresso
A estrutura de dissipação de calor do substrato de cerâmica é a estrutura da camada de circuito - base de cerâmica - camada de placa de circuito. Como não há uma camada isolante no meio, o calor do dispositivo é transferido diretamente da base de cerâmica para a camada de circuito e a dissipação de calor é externa, a dissipação de calor é rápida e o efeito é bom. A placa de circuito impresso é a necessidade de calor da camada média - camada de isolamento - camada de linha, separada por uma camada de isolamento ao mesmo tempo, a própria camada dielétrica da condutividade térmica é ruim e, em seguida, adiciona adesivo de condução de calor, o efeito de condução de calor ainda não foi aprimorado e, muitas vezes, não consegue atingir o objetivo do dispositivo de dissipação rápida de calor. Em particular, alguns dispositivos de alta potência precisam usar o substrato de cerâmica como substrato de resfriamento no campo de produtos em que a dissipação de calor e a mudança de temperatura são relativamente grandes.
(4) A aplicação do substrato de cerâmica e da placa de circuito impresso é diferente
A aplicação do substrato cerâmico e da placa de circuito impresso é diferente, principalmente o desempenho dos dois é diferente, o substrato cerâmico é usado em alta condutividade térmica, alta dissipação de calor, alto isolamento, campo de produto, como iluminação LED de alta potência, módulo de alta potência, comunicação de alta frequência, fonte de alimentação de trilha; A placa de circuito impresso comum é usada em alguns requisitos mais extensos, de dissipação de calor, isolamento e outros não são rigorosos, usados em mercadorias comerciais privadas.
(5) O preço do substrato de cerâmica é diferente do preço da placa de circuito impresso
O material e o desempenho do substrato de cerâmica e da placa de circuito impresso são diferentes, e a decisão final é que seus preços são diferentes. A placa de substrato de cerâmica é muito alta e o custo de produção é alto.
O substrato de cerâmica tem vantagens excepcionais, mas é frágil e tem uma alta taxa de refugo, o que exige um alto nível de tecnologia de produção. No entanto, não é possível fazer uma placa de circuito com tamanho superior a um metro, como as placas de circuito impresso comuns. A Hitech Circuits tem mais de 10 anos de experiência no setor de placas de circuito de cerâmica, e muitas universidades e instituições de P&D estão em cooperação.
2. Diferença entre o substrato de cerâmica e a placa de alta frequência
O material é diferente. O substrato de cerâmica é feito de óxido de alumínio ou nitreto de alumínio, e a placa de alta frequência é feita de Rogers, Yaron, PTFE, etc., com baixa constante dielétrica e alta velocidade de comunicação de frequência.
O desempenho é diferente. O substrato de cerâmica é amplamente utilizado em sistemas e refrigeração, módulos de alta potência, eletrônica automotiva e outros campos. A placa de alta frequência é usada principalmente no campo de comunicação de alta frequência, aviação, eletrônicos de consumo de ponta e assim por diante. O campo de comunicação de alta frequência envolve requisitos de dissipação de calor e geralmente precisa ser combinado com a base de cerâmica e a placa de alta frequência, como a placa de circuito impresso de cerâmica de alta frequência.
1. Aplicação do substrato de cerâmica
Os substratos de cerâmica são usados em chips de led para obter melhor condutividade térmica. Além disso, o substrato de cerâmica também é usado para fabricar chips de cerâmica nos seguintes dispositivos eletrônicos:
Módulo semicondutor de alta potência
Resfriador de semicondutor, aquecedor eletrônico; circuito de controle de potência, circuito de mistura de potência
Módulo de energia inteligente; fonte de alimentação de comutação de alta frequência, relé de estado sólido
Componentes eletrônicos automotivos, aeroespaciais e militares
(1) Aplicação de substrato de cerâmica em semicondutores de terceira geração
Os principais dispositivos de energia representados por MOSFET, IGBT e transistor ocupam um lugar em seus próprios segmentos de frequência e fonte de alimentação. Devido ao excelente desempenho abrangente do IGBT, ele substituiu o GTR e se tornou o inversor, o UPS, o conversor de frequência, o acionamento do motor, a fonte de alimentação de comutação de alta potência, especialmente agora o veículo elétrico quente, o trilho de alta velocidade e outros dispositivos eletrônicos de potência nos dispositivos principais.
(2)Aplicação do substrato de cerâmica de alumina no campo da energia eletrônica
No campo da eletrônica de potência, como fonte de alimentação de comutação de potência, acionamento elétrico etc., o substrato de cerâmica dielétrica é necessário para obter melhor condutividade térmica, evitar a queima de corrente e curto-circuito.
Com a recomendação de inteligência artificial e proteção ambiental, a indústria automobilística também lançou carros elétricos, principalmente por meio do armazenamento de baterias. As baterias de lítio feitas de substrato de cerâmica podem alcançar melhores funções de dissipação de calor e corrente, promovendo a demanda do mercado por novos veículos de energia.
2. Vantagens do substrato de cerâmica
A. O coeficiente de expansão térmica do substrato de cerâmica é próximo ao do chip de silício, o que pode economizar a folha Mo da camada de transição, economizar mão de obra, economizar material e reduzir o custo;
B. Reduzir a camada de solda, reduzir a resistência térmica e reduzir a cavidade;
C. Sob o mesmo fluxo de carga, a largura do fio da folha de cobre de 0,3 mm de espessura é apenas 10% da largura da placa de circuito impresso comum;
D. Excelente condutividade térmica, de modo que a embalagem do chip é muito compacta, o que aumenta muito a densidade de potência e melhora a confiabilidade do sistema e do dispositivo;
E. O substrato de cerâmica ultrafino (0,25 mm) pode substituir o BeO, sem problemas de toxicidade ambiental;
F. Grande capacidade de carga, corrente de 100 A passando continuamente por um corpo de cobre de 1 mm de largura e 0,3 mm de espessura, aumento de temperatura de cerca de 17 ℃; com corrente de 100 A passando continuamente por um corpo de cobre de 2 mm de largura e 0,3 mm de espessura, o aumento de temperatura é de apenas cerca de 5 ℃.
G. Baixa resistência térmica, substrato de cerâmica de 10×10mm 'resistência térmica de 0,63mm de espessura do substrato de cerâmica é de 0,31K/W, 0,38mm de espessura do substrato de cerâmica é de 0,19K/W, 0,25mm de espessura do substrato de cerâmica é de 0,14K/W.
H. Alto isolamento e resistência a alta pressão para garantir a segurança pessoal e a proteção do equipamento.
I. Novos métodos de embalagem e montagem podem ser realizados, de modo que o produto é altamente integrado e o tamanho é reduzido.
3. Tecnologia de substrato de cerâmica
Atualmente, os tipos comuns de substrato de cerâmica para dissipação de calor incluem HTCC, LTCC, DBC e DPC. O DBC é o uso da combinação de placas de Al2O3 e de Cu para aquecimento em alta temperatura; seu gargalo técnico não é fácil de resolver o problema dos microporos entre as placas de Al2O3 e de Cu, o que torna a produção em massa de energia e o rendimento do produto um grande desafio. A tecnologia DPC é o uso da tecnologia de revestimento direto de cobre, deposição de cobre no substrato de Al2O3, seu processo combinado com a tecnologia de material e filme, seu produto é o substrato de resfriamento de cerâmica mais comumente usado nos últimos anos. No entanto, seus requisitos de capacidade de integração de tecnologia de processo e controle de material são altos, o que faz com que o limiar técnico de entrada no setor de DPC e a produção estável sejam relativamente altos.
(1) HTCC (cerâmica co-queimada de alta temperatura)
O processo de fabricação do HTCC é muito semelhante ao do LTCC. A principal diferença é que o pó cerâmico do HTCC não é adicionado com material de vidro. Portanto, o pó cerâmico do HTCC deve ser seco e endurecido em forma embrionária a uma temperatura alta de 1300~1600℃. Devido à sua alta temperatura de co-combustão, a escolha de materiais condutores de metal é limitada, seus principais materiais para alto ponto de fusão, mas baixa condutividade são tungstênio, molibdênio, manganês... Como o metal e, por fim, a moldagem por sinterização laminada.
(2) LTCC (cerâmica co-queimada de baixa temperatura)
O LTCC também é conhecido como substrato cerâmico multicamadas coqueado de baixa temperatura. Nessa tecnologia, o pó de óxido de alumínio inorgânico e cerca de 30% a 50% de material de vidro são combinados com um aglutinante orgânico para que sejam misturados uniformemente em uma pasta de lama. Em seguida, a lama é raspada em folhas com um raspador e, depois, por meio de um processo de secagem, a lama da folha é formada em uma peça fina de peça bruta. Como a transmissão de sinais em todos os níveis
Para as linhas internas do LTCC, a tecnologia de serigrafia é usada para preencher buracos e imprimir linhas nos embriões brutos, e os eletrodos internos e externos podem ser usados, respectivamente, de prata, cobre, ouro e outros metais. Por fim, as camadas são empilhadas e sinterizadas em um forno de sinterização a 850~900°C.
(3) Cobre com ligação direta (DBC)
A tecnologia de revestimento de cobre direto é o uso de líquido eutético de cobre e oxigênio diretamente no revestimento de cerâmica. O princípio básico é introduzir uma quantidade adequada de oxigênio entre o cobre e a cerâmica antes ou durante o processo de revestimento, na faixa de 1065℃~1083℃, O cobre e o oxigênio formam o líquido eutético Cu-O. A tecnologia DBC usa a solução eutética para reagir quimicamente com o substrato de cerâmica para formar a fase CuAlO2 ou CuAl2O4, por um lado, e para infiltrar a folha de cobre para realizar a combinação do substrato de cerâmica e da placa de cobre, por outro lado.
(4) DPC (Direct Plate Copper)
O DPC também é conhecido como substrato banhado a cobre direto. Veja o processo do substrato DPC como exemplo: Em primeiro lugar, o substrato de cerâmica é pré-tratado e limpo, e o substrato de cerâmica é pulverizado no substrato de cerâmica e combinado com a camada composta de cobre usando a tecnologia de revestimento a vácuo da fabricação de filmes finos. Em seguida, o circuito é feito pelo processo de reexposição, revelação, gravação e remoção de filme com a fotorresistência de micro-sombra de luz amarela. Por fim, a espessura do circuito é aumentada pela deposição de galvanoplastia/galvanização sem eletrólito, e o circuito metalizado é feito após a remoção da fotorresistência.
3. Processo de produção de substrato de cerâmica
1. Perfuração
Em comparação com a tecnologia de perfuração tradicional, a tecnologia de perfuração a laser tem as vantagens de alta precisão, velocidade rápida, alta eficiência, perfuração em massa em grande escala, adequada para a grande maioria dos materiais duros e macios, sem perda de ferramentas, em linha com a interconexão de alta densidade da placa de circuito impresso, desenvolvimento fino.
O processo de perfuração a laser do substrato cerâmico tem alta força de ligação da cerâmica e do metal, sem queda, fenômeno de formação de espuma, para obter o efeito de crescimento conjunto, alta suavidade da superfície, rugosidade de 0,1 μm a 0,3 μm, abertura de perfuração a laser de 0,15 mm a 0,5 mm, podendo até chegar a 0,06 mm.
2、Revestimento de cobre
O revestimento de cobre refere-se à área sem fiação na placa de circuito coberta com folha de cobre, conectada ao fio terra, a fim de aumentar a área do fio terra, reduzir a área de loop, reduzir a queda de tensão, melhorar a eficiência energética e a capacidade anti-interferência. O revestimento de cobre pode não apenas reduzir a impedância de aterramento, mas também reduzir a área da seção transversal do loop e melhorar o loop de espelho do sinal. Portanto, o processo de revestimento de cobre desempenha um papel muito importante no processo de PCB de substrato de cerâmica. Um loop de espelho incompleto e truncado ou a posição incorreta da camada de cobre geralmente levam a novas interferências e têm um impacto negativo no uso da placa.
3. Gravura
Os substratos cerâmicos também precisam ser gravados, com o padrão do circuito pré-revestido com uma camada de resistência de chumbo-estanho e, em seguida, gravado quimicamente para remover o cobre desprotegido e não condutor para formar o circuito. A gravação é dividida em gravação da camada interna e gravação da camada externa; a gravação da camada interna usa gravação ácida, com filme úmido ou seco como resistência à corrosão; a gravação externa é alcalina, com estanho e chumbo como resistência.
Há muitos tipos de processos de fabricação de produtos cerâmicos na fábrica de placas de circuito. Diz-se que há mais de 30 tipos de processos de fabricação, como prensagem a seco, rejuntamento, extrusão, injeção, fundição e prensagem isostática. Como o substrato de cerâmica eletrônica é do tipo "plano", a forma não é complicada, o processo de fabricação de moldagem e processamento a seco é simples e o custo é baixo, portanto, a maioria deles usa o método de moldagem por prensagem a seco. O processo de fabricação da cerâmica eletrônica PCB por prensagem a seco inclui principalmente a formação de peças em branco, a sinterização de peças em branco e o acabamento, formando o circuito no substrato.
4. Fabricação ecológica de substrato de cerâmica (formação)
Use pó de alumina de alta pureza (teor ≥95% de Al2O3) (diferentes tamanhos de partículas são necessários, dependendo da finalidade e do método de fabricação. Por exemplo, de alguns analfabetos a dezenas de mícrons) e aditivos (principalmente adesivos, dispersantes, etc.). Formar uma "pasta" ou material processado.
(1) Prensagem a seco do substrato cerâmico para produzir peças verdes (ou "verdes")
O tarugo de prensagem a seco é o uso de alumina de alta pureza (cerâmica eletrônica com teor de alumina superior a 92%, a maior parte do uso de 99%) em pó (as partículas de prensagem a seco não devem exceder 60μm, para extrusão, laminação, injeção e outras partículas de pó devem ser controladas dentro de 1μm), adicione a quantidade adequada de plastificante e aglutinante, misturado uniformemente após o tarugo de prensagem a seco. No momento, a prole de peças quadradas ou redondas pode atingir 0,50 mm ou até mesmo ≤0,3 mm (dependendo do tamanho da placa). Os tarugos prensados a seco podem ser processados antes da sinterização, como dimensionamento e perfuração. Usinagem, mas tenha cuidado para compensar o encolhimento do tamanho causado pela sinterização (amplie o tamanho do encolhimento).
(2) Produção de tarugo verde pelo método de espalhamento de substrato cerâmico
Fluxo de cola líquida (pó de óxido de alumínio + solvente + dispersante + adesivo + plastificante misturados uniformemente + peneiramento) fabricação + fluxo de fundição (na cola da máquina de fundição de fluxo em metal ou cinto de poliéster resistente ao calor) + secagem + corte (também pode ser outro processamento) + desengorduramento + sinterização e outros processos. Ele pode realizar automação e produção em escala.
(3) Sinterização e acabamento do tarugo verde após a sinterização
As peças brutas do substrato de cerâmica geralmente precisam ser "sinterizadas" e receber acabamento após a sinterização. A "sinterização" do tarugo de cerâmica refere-se ao processo de "sinterização", o tarugo (volume) na cavidade, o ar, as impurezas e a matéria orgânica, como a remoção por pressão a seco, de modo que sua volatilização, combustão, extrusão e remoção de partículas de alumina. Obtenha contato próximo ou processo de crescimento combinado, portanto, após a sinterização do tarugo verde de cerâmica, haverá perda de peso, encolhimento do tamanho, deformação da forma, aumento da resistência à compressão, redução da porosidade e outras alterações.
Os métodos de sinterização do tarugo de cerâmica são os seguintes ① sinterização atmosférica, sinterização sem pressão trará grande deformação; ② sinterização por pressão (prensagem a quente), sinterização por pressão, pode obter bons produtos planos é o método mais comumente usado; ③ sinterização isostática a quente é o uso de sinterização a gás quente de alta pressão. Seus produtos característicos são acabados na mesma temperatura e pressão. Todos os tipos de equilíbrio de desempenho, o custo é relativamente alto. No valor agregado dos produtos, ou produtos aeroespaciais, de defesa nacional e militares no uso desse método de sinterização, como o campo militar de espelhos, combustível nuclear, barris e outros produtos. A temperatura de sinterização dos tarugos verdes de alumina prensados a seco está, em sua maioria, entre 1.200°C e 1.600°C (dependendo da composição e do fluxo).
(4) Acabamento do substrato cerâmico após a sinterização (cozido) em branco
A maioria dos tarugos cerâmicos sinterizados precisa de acabamento. O objetivo é: ① obter uma superfície plana. No processo de sinterização em alta temperatura do tarugo verde, devido ao desequilíbrio da distribuição de partículas, vazios, impurezas e matéria orgânica no tarugo verde, isso causará deformação, irregularidade ou rugosidade e diferença excessivas. Esses defeitos podem ser resolvidos com o acabamento da superfície; ② Obter superfície de alto acabamento, como reflexão especular, ou melhorar a lubrificação (resistência ao desgaste).
O tratamento de polimento de superfície consiste em usar materiais de polimento (como carbeto de silício, B4C) ou pasta de areia de diamante para polir gradualmente a superfície, de abrasivo grosso a fino. De modo geral, o uso de pó de AlO ou pasta de diamante ≤1μm, ou processamento a laser ou ultrassônico para alcançar.
(5) tratamento forte (aço)
Após o polimento da superfície, a fim de melhorar a resistência mecânica (como resistência à flexão etc.), o revestimento a vácuo por raios eletrônicos, o revestimento a vácuo por pulverização catódica, a evaporação de vapor químico e outros métodos podem ser usados para revestir uma camada de filme composto de silício, por meio de tratamento térmico de 1200°C a 1600°C, o que pode melhorar significativamente a resistência mecânica das peças de cerâmica!
5. Formar um padrão condutor (circuito) no substrato
Para processar gráficos condutores (circuitos) em substratos de cerâmica, é necessário primeiro fabricar substratos de cerâmica revestidos de cobre e, em seguida, fabricar placas de circuito impresso de cerâmica de acordo com a tecnologia de PCB.
(1) Formação de um substrato de cerâmica revestido de cobre. Atualmente, há dois métodos de formação de substratos de cerâmica revestidos de cobre
① Método de laminação. É formado pela prensagem a quente de um lado da folha de cobre oxidada e do substrato de cerâmica de alumina. Ou seja, a superfície da cerâmica é tratada (como laser, plasma, etc.), obtém-se uma superfície ativada ou áspera e, em seguida, de acordo com a laminação "folha de cobre + camada de aglutinante resistente ao calor + cerâmica + camada de aglutinante resistente ao calor + folha de cobre", após sinterização de 1020°C ~ 1060°C, a formação de laminado cerâmico revestido de cobre de dupla face. ② Método de galvanoplastia. Após o tratamento de plasma, o substrato de cerâmica é "filme de titânio pulverizado + filme de níquel pulverizado + filme de cobre pulverizado" e, em seguida, cobre de galvanoplastia convencional até a espessura de cobre necessária, ou seja, a formação de substrato de cerâmica revestido de cobre de dupla face.
(2) Fabricação de placas de circuito impresso de cerâmica de face simples e dupla
De acordo com as técnicas tradicionais de fabricação de PCBs, são usados substratos cerâmicos revestidos de cobre de face simples e dupla
(3) Fabricação de placas de cerâmica multicamadas
Em painéis simples e duplos, camada de isolamento repetidamente revestida (alumina), sinterização, fiação, sinterização para formar placa de PCB multicamadas ou o uso de tecnologia de fabricação de fundição para completar. ② A placa multicamada de cerâmica é fabricada pelo método de fundição. A fita bruta é formada na máquina de fundição e, em seguida, é feita a perfuração, o encaixe (cola condutora, etc.), a impressão (circuito condutor, etc.), o corte, a laminação e a prensagem isostática para formar a placa multicamadas de cerâmica. A Hitech Circuits tem mais de 10 anos de experiência na fabricação de substratos de cerâmica, portanto, sinta-se à vontade para consultá-la se precisar de mais informações técnicas.
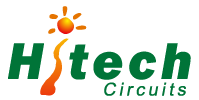
+86-755-29970700 or +86-(0)18033052758
sales@hitechpcb.com
2F, Building C, Suojia Technology Park, Hangcheng, Bao’an, Shenzhen, Guangdong, China 518126