Processo de Montagem de PCB
Processo de Montagem de PCB
Em primeiro lugar, levá-lo a conhecer uma breve história de desenvolvimento de PCBA, também chamado de montagem PCB. PCBA é a abreviatura, o que significa que o processo SMT do PCB terminou ou o processo de passagem pelo DIP ou THT. Em seguida, é abreviado como PCBA. De facto, é comummente designada por placa eletrónica ou placa de circuitos.
A placa de circuito impresso, abreviada como PCB, é um importante componente eletrónico e o suporte de componentes electrónicos. Esta é a versão mais antiga. Mais tarde, os austríacos criaram novas tecnologias que removeram metais indesejados e acrescentaram cablagem, formando a versão que utilizamos atualmente.
Devido à sua posição na segunda metade do processo do equipamento eletrónico, o PCBA é referido como a jusante da indústria eletrónica. Uma vez que todos os dispositivos e equipamentos electrónicos requerem o apoio do PCBA, este projeto tem a maior parte do mercado eletrónico. Atualmente, existem enormes áreas industriais em todo o mundo que fabricam placas de circuito impresso (PCB).
Os computadores e produtos afins, os dispositivos de comunicação e os dispositivos electrónicos são os principais grupos de consumidores de PCBA. Incluindo os computadores normalmente utilizados em casa, televisores, luzes LED, telemóveis, tablets, etc. Devido ao facto de todos os agregados familiares o utilizarem, o desenvolvimento económico do PCBA é rápido e tornou-se rapidamente o mais importante do mundo.
O PCBA ainda está em desenvolvimento e, para tornar a vida das pessoas mais conveniente, existem várias condições gerais para o seu desenvolvimento:
a. Desenvolver vigorosamente o HDI para tornar os PCB mais precisos e mais pequenos.
b. O PCBA também precisa garantir forte vitalidade e vida útil para durar mais tempo.
c. Atualizar o equipamento de produção e o processo de fabrico.
No processamento de PCBA, são utilizados componentes SMD e componentes de encaixe (THT, Through-hole technology).
Capítulo 1: Componentes SMD e Componentes de Encaixe (THT)
Então, qual é a diferença entre os componentes SMD e os componentes plug-in (THT)?
1 、 A diferença entre os dois é a seguinte:
1.1 Os componentes SMD têm tamanho pequeno, peso leve e são mais fáceis de soldar do que os componentes plug-in.
1.2 Um benefício importante dos componentes SMD é que eles melhoram a estabilidade e a confiabilidade do circuito; Como o componente SMD não possui fios, ele reduz os campos elétricos e magnéticos dispersos, o que é particularmente eficaz em circuitos analógicos de alta frequência e circuitos digitais de alta velocidade.
2 、 Método de solda para ambos
2.1 Método para soldar componentes SMD:
Coloque o componente na almofada de solda, aplique a pasta de solda SMD preparada na superfície do componente e na área de contato entre a almofada de solda e, em seguida, aqueça a conexão entre a almofada de solda e o componente SMD com um ferro de solda elétrico de aquecimento interno de 20W (a temperatura deve estar entre 220 ~ 230 ℃). Depois que a solda derreter, remova o ferro de solda elétrico e aguarde a solidificação da solda antes que a soldagem seja concluída. Após a soldadura, pode ser utilizada uma pinça para fixar os componentes soldados para verificar se existe alguma folga. Se não houver folga, significa que a soldadura está boa. Se houver folga, reaplicar a pasta de solda e soldar novamente de acordo com o método acima.
2.2 Método para soldar componentes THT:
Ao soldar todos os pinos, a solda deve ser adicionada à ponta do ferro de soldar e o fluxo deve ser aplicado a todos os pinos para os manter húmidos. Tocar a extremidade de cada pino do chip com a ponta do ferro de soldar até que a solda flua para os pinos. Depois de todos os pinos estarem soldados, humedecer os pinos com fluxo para limpar o estanho de soldadura, de modo a eliminar qualquer curto-circuito e sobreposição. Por fim, utilizar uma pinça para verificar se a soldadura está defeituosa. Após a inspeção, retirar o fluxo da placa de circuitos e limpar cuidadosamente a escova dura ao longo da direção dos pinos com álcool até o fluxo desaparecer.
Capítulo 2: Processo Completo de PCBA
Depois de aprender algo sobre os componentes, eis um processo completo de montagem da placa PCB:
Passo 1: Aplicar a pasta de solda na placa PCB
Nesta etapa, obviamente, será utilizado o estêncil de aço inoxidável e a pasta de solda.
A pasta de solda deve ser aplicada uniformemente à placa de circuito impresso nos PADs correctos e nos locais necessários.
Passo 2: Utilizar a máquina de montagem para selecionar e colocar
Os componentes montados à superfície, ou SMD, devem ser colocados numa placa de circuito impresso preparada por uma máquina de montagem automática. Em seguida, os componentes têm de ser soldados nas almofadas correctas das placas de circuitos.
Passo 3: Passar pelo refluxo para soldar os componentes
Este processo ajudará a solidificar a pasta de solda e, para aderir os componentes à placa de circuito impresso, a pasta de solda tem de entrar no refluxo e permanecer durante um período de tempo para obter uma melhor soldadura.
Passo 4: Inspecionar o conjunto de PCB semi-acabado
Uma vez terminado o processo de refluxo e soldados os componentes de montagem no local correto, procede-se à inspeção atual da placa de circuito impresso durante a fase SMT. A placa montada deve ser testada e inspeccionada quanto à sua funcionalidade, por exemplo, utilizando gabaritos ICT, AOI, etc.
As formas de verificar a qualidade do PCBA incluem os seguintes aspectos básicos:
Inspeção manual: O trabalhador da produção e a pessoa do departamento de qualidade devem efetuar uma inspeção visual para garantir a boa qualidade de uma PCB.
Inspeção ótica automática (designada por AOI): Um método de inspeção e uma determinada máquina mais adequados para lotes maiores de PCBAs. Uma máquina de inspeção ótica automática, ou máquina AOI, utiliza câmaras de alta potência, colocadas em diferentes ângulos para visualizar as ligações de solda.
Inspeção por raios X: Uma máquina de inspeção utilizada para PCBs mais complexas, examinando as camadas da PCB e identificando potenciais problemas, especialmente para as que têm BGAs, QFNs, etc.
Etapa 5: Inserir o componente com orifício de passagem
Um orifício de passagem revestido, ou PTH, é um orifício na placa de circuito impresso. É revestido através da placa. Em vez de pasta de soldadura, é necessário um método de soldadura mais especializado para este processo. Geralmente, depois de inserir os componentes no orifício, as placas são colocadas na soldadura por onda
Soldadura manual: para a placa simples, por vezes pode ser utilizada a soldadura manual, mas não é recomendada a todo o momento.
Soldadura por onda: A versão automatizada da soldadura manual, em que uma onda de solda derretida solda todos os orifícios que exigem a soldadura na parte inferior da placa de uma só vez.
Passo 6: Concluir a inspeção final
Quando todo o processo de soldadura da montagem da placa de circuito impresso estiver concluído e terminado, é altura de efetuar uma inspeção final e um teste funcional. Isto dependerá dos requisitos dos diferentes projectos e dos diferentes clientes. Inclui o teste ICT e o teste FCT.
Executar sinais de potência e simulados para testar as características eléctricas das PCB. Um sinal de que a PCB falhou é quando mostra a flutuação dos sinais eléctricos durante o teste.
Se a placa de circuito impresso falhar durante a inspeção final, deve ser novamente verificada e testada. E o processo recomeça até que seja produzida uma PCB boa e bem sucedida.
Capítulo 3: Algumas Tecnologias Especiais em SMT
A soldadura por refluxo é utilizada para derreter a pasta de solda para soldar e fixar componentes electrónicos. A soldadura por refluxo está dividida em quatro zonas de temperatura, nomeadamente zonas de pré-aquecimento, temperatura constante, aquecimento e arrefecimento.
Cada zona de temperatura tem funções diferentes. A soldadura por refluxo normal é principalmente a soldadura por refluxo a ar, que lida com produtos electrónicos comuns, enquanto os produtos com elevados requisitos de qualidade, estabilidade e taxa de vazios (como a eletrónica automóvel, a aviónica, a eletrónica médica, etc.) necessitarão de soldadura por refluxo a nitrogénio, mesmo a soldadura por refluxo a vácuo. Isto significa introduzir o azoto durante a soldadura por refluxo.
Na soldadura por refluxo, o azoto é normalmente utilizado nas zonas de aquecimento e de arrefecimento. Por que razão é necessário adicionar azoto? Vamos falar sobre este assunto aqui.
Existem três razões principais para adicionar nitrogénio à soldadura por refluxo.
1. Reduzir a oxidação
2. Aumentar a molhabilidade e melhorar a qualidade da soldadura
3. Reduzir a fração de vazio
Os pormenores que se seguem:
1. Reduzir a oxidação do forno
Como o nitrogênio é um gás inerte, após a adição de nitrogênio, o fundo do refluxo é ocupado por nitrogênio, isolando o oxigênio no fundo do refluxo, reduzindo assim o contato com o oxigênio e reduzindo a reação de oxidação do PCBA através do refluxo.
2. Aumentar a molhabilidade e melhorar a qualidade da soldadura
O gás nitrogénio ocupa a parte inferior da zona de temperatura de aquecimento, o que aumenta a molhabilidade da pasta de solda durante a fusão a quente a altas temperaturas. Isto permite que vários componentes sejam soldados melhor e garante a melhoria da qualidade da soldadura.
Teste e Inspeção de Montagem de PCB
O teste PCBA refere-se ao teste de condutividade eléctrica e valor de entrada-saída com base na placa PCBA com componentes electrónicos.
Por que razão são necessários testes PCBA?
Na conceção da PCB, existe uma relação numérica entre diferentes pontos de teste, como a tensão e a corrente. No entanto, o fluxo do processo de produção e processamento de PCBA é muito complexo, incluindo muitos processos importantes, como o processo de fabrico de PCB, aquisição e inspeção de componentes, montagem de patches SMT, teste de PCBA de encaixe. No processo de produção e processamento, podem ocorrer vários problemas devido a equipamento ou operação inadequados. Por conseguinte, é necessário utilizar equipamento de teste profissional ou um multímetro manual para testar os pontos de teste, para verificar se a placa PCBA real cumpre os requisitos de conceção e garantir que cada produto não terá problemas de qualidade.
O teste PCBA é um passo fundamental para garantir a qualidade da produção e entrega. O dispositivo de teste FCT é feito de acordo com o programa de pontos de teste e as etapas de teste projetadas pelos clientes e, em seguida, a placa PCBA é colocada no rack de teste FCT para concluir o teste.
O teste é crucial para garantir que produtos de alta qualidade sejam entregues aos clientes. Felizmente, os montadores de placas oferecem várias camadas de teste e inspeção para garantir a produção e a entrega de placas de circuito montadas de alta qualidade aos clientes. Apesar de todos os esforços para evitar erros, a montagem de placas de circuitos impressos é um processo complexo e, por vezes, ocorrem defeitos relacionados com uma variedade de questões, desde o carregamento incorreto de componentes a falhas no equipamento SMT. São efectuados testes e inspecções minuciosos ao longo do processo de produção para garantir que os problemas são detectados numa fase inicial, assegurando uma elevada qualidade e rendimento.
Breve Análise de Três Processos de Estêncil para PCB
1. Estêncil de Pasta de Solda: Como o nome sugere, é utilizado para escovar a pasta de solda. Fazer furos numa chapa de aço correspondentes à almofada de solda da placa de circuito impresso. Em seguida, utilizar pasta de solda para transferir e imprimir na placa de circuito impresso através de um estêncil. Ao imprimir pasta de solda, a pasta de solda é aplicada acima do estêncil, enquanto a placa de circuito impresso é colocada abaixo do estêncil. Em seguida, utiliza-se um raspador para raspar a pasta de solda uniformemente nos orifícios do estêncil (quando a pasta de solda é espremida, escorrerá dos orifícios do estêncil e cobrirá a placa de circuito impresso). Colocar os componentes SMD e realizar a soldadura por refluxo uniformemente. Os componentes de encaixe são soldados manualmente.
2. Estêncil de Cola Vermelha: A abertura é feita entre as duas almofadas do componente com base no tamanho e no tipo da peça. Utilizando a dispensa de cola (que usa ar comprimido para aplicar cola vermelha no substrato através de uma cabeça dispensadora de cola dedicada), a cola vermelha é transferida para a placa PCB através de pontos de estêncil. Em seguida, inserir os componentes, aguardar que os componentes adiram firmemente à placa de circuito impresso e, depois, inserir os componentes de encaixe para a soldadura por onda unificada.
3. Estêncil de Processo Duplo: Quando uma placa de circuito impresso precisa de ser revestida com pasta de solda e cola vermelha, é necessário utilizar o estêncil de processo duplo. O estêncil de processo duplo consiste em dois estêncis, um estêncil a laser comum e um estêncil de passo. Como determinar se a pasta de solda utiliza o estêncil escalonado ou a cola vermelha utiliza o estêncil escalonado? Em primeiro lugar, é necessário saber se se deve aplicar primeiro a pasta de solda ou a cola vermelha. Se a pasta de solda for aplicada primeiro, o estêncil de pasta de solda é transformado num estêncil laser normal e o estêncil de cola vermelha é transformado num estêncil escalonado. Se a cola vermelha for aplicada em primeiro lugar, o estêncil de cola vermelha é transformado num estêncil a laser normal e o estêncil de pasta de solda é transformado num estêncil escalonado.
A qualidade do estêncil de aço inoxidável para PCB é afetada principalmente pelos seguintes factores
1. Processo de Produção
Anteriormente, discutimos o processo de produção de estêncil de aço inoxidável, e pode ser visto que o melhor processo deve ser o corte a laser de estêncil de aço inoxidável seguido de tratamento de polimento elétrico. A gravação química e a eletrodeposição têm ambos processos propensos a erros, como a produção de películas de longevidade, a exposição e o desenvolvimento, e a eletrodeposição é também afetada por substratos irregulares.
2. Materiais Utilizados
Incluindo a estrutura da placa de circuito impresso, a rede metálica, a chapa de aço, o adesivo, etc. A estrutura de malha de PCB deve ser capaz de suportar determinados relés de programa e ter um bom nivelamento; é preferível utilizar malha de poliéster, uma vez que pode manter uma tensão estável durante muito tempo; é preferível utilizar chapas de aço de grau 304, e as chapas mate serão mais propícias à laminagem de pasta de solda (adesivo) do que as chapas espelhadas; o adesivo deve ter resistência suficiente e ser capaz de suportar determinada corrosão.
3. Desenho da Abertura
A qualidade do desenho da abertura tem o maior impacto na qualidade do estêncil de aço inoxidável para PCB. Como discutido anteriormente, o design das aberturas deve considerar o processo de produção, a relação de aspeto, a relação de área, o valor da experiência, etc.
4. Materiais de Produção
A exaustividade dos materiais de produção também pode afetar a qualidade do estêncil de aço inoxidável para PCB. Quanto mais completa for a informação, melhor. Ao mesmo tempo, quando os dados coexistem, deve ficar claro qual deles deve prevalecer. Além disso, de um modo geral, a utilização de ficheiros de dados para criar estêncil de aço inoxidável pode minimizar os erros tanto quanto possível.
5. Método de Utilização
O método de impressão correto pode manter a qualidade do stencil de aço inoxidável. Por outro lado, métodos de impressão incorrectos, como pressão excessiva ou estêncil de aço inoxidável PCB irregular ou PCB durante a impressão, podem causar danos no estêncil de aço inoxidável.
6. Limpeza
A pasta de solda (adesivo) é relativamente fácil de solidificar e, se não for limpa atempadamente, bloqueará a abertura do estêncil de aço inoxidável, dificultando a impressão da próxima vez. Por conseguinte, depois de retirar o estêncil de aço inoxidável para PCB da máquina ou de não imprimir pasta de solda na máquina de impressão durante 1 hora, esta deve ser limpa atempadamente.
7. Armazenamento
O estêncil de aço inoxidável deve ser armazenado num local específico e não deve ser colocado aleatoriamente para evitar danos acidentais no estêncil de aço inoxidável. Ao mesmo tempo, o stencil de aço inoxidável para PCB não deve ser empilhado em conjunto, uma vez que é difícil de manusear e pode dobrar a estrutura da rede.
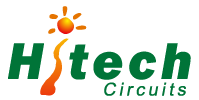
+86-755-29970700 or +86-(0)18033052758
sales@hitechpcb.com
2F, Building C, Suojia Technology Park, Hangcheng, Bao’an, Shenzhen, Guangdong, China 518126